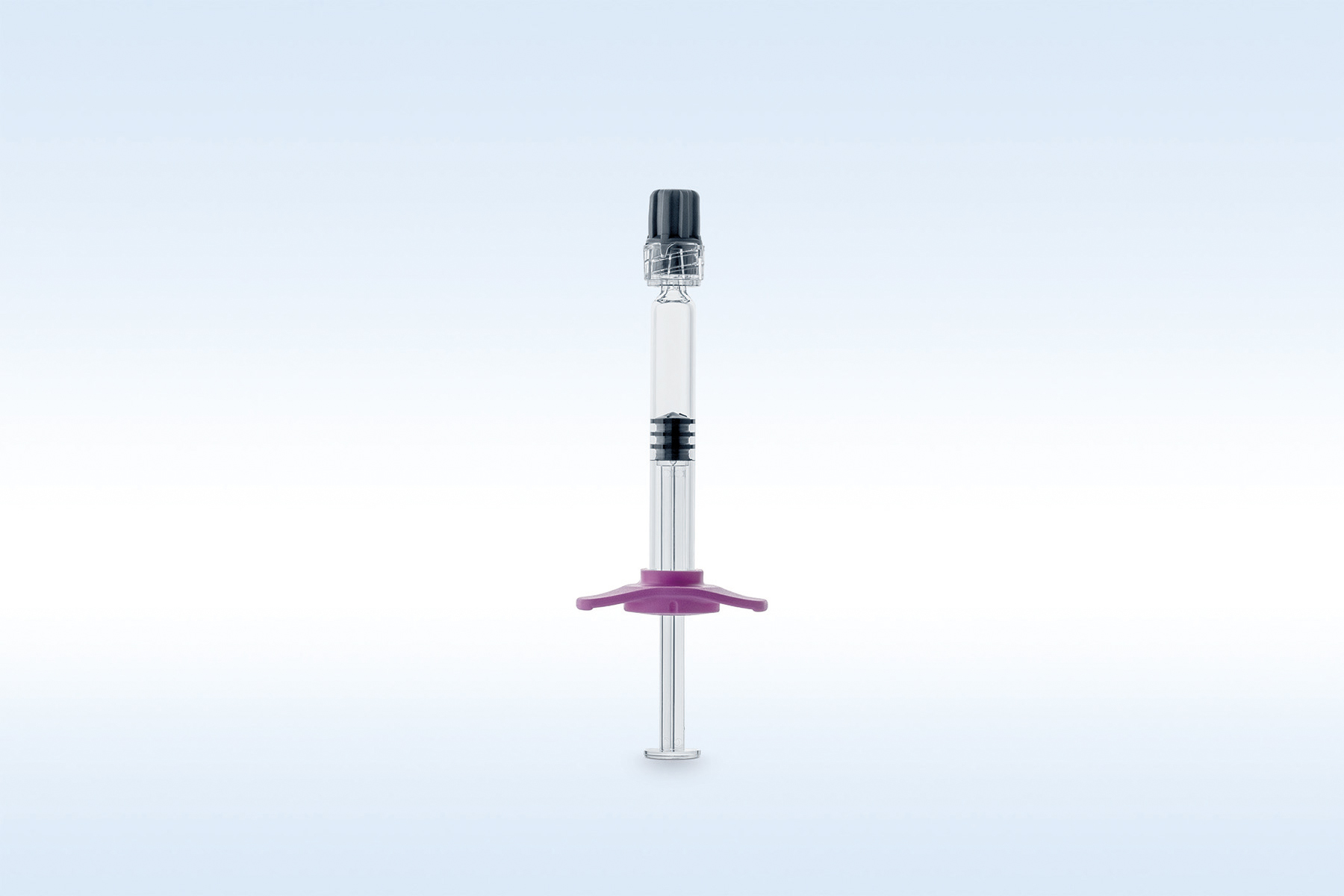
Hot steam sterilizable, impact resistant and dimensionally stable
Simplified manufacturing process using 2-component injection molding technology
Comprehensive customer service for component development
Pittsburgh, January 31, 2019 — The market for prefilled syringes is currently experiencing strong growth – for example, in systems for the treatment of chronic diseases such as rheumatism. The design of such injection systems is primarily concerned with ease of use to ensure that the patient is reliably supplied with the intended dose of the active substance. The adapter for screwing in the needle and the syringe cap plays a key role.
With Gx TELC (Tamper Evident Luerlock Closure), Gerresheimer AG is offering an integrated solution which combines both functions in a single component and also enables tamper-evident protection of the active ingredient. The medical technology specialist based in Düsseldorf chose Apec® 1745 high heat polycarbonate from Covestro as the material for the adapter. For the first time, the company is participating in the Pharmapack 2019 trade fair on February 6 and 7 in Paris, and will present this development at its booth number C94.
Resistant to high temperatures and impacts
The transparent high-temperature polycarbonate is characterized by its high heat resistance and can be sterilized using conventional methods such as gamma rays or ethylene oxide. "In addition, it is dimensionally stable and dimensionally accurate at high temperatures, so that the entire component does not warp after hot steam sterilization at 143 °C, for example. As a result, the closure for opening the syringe remains defined in every situation and enables an easy screwing in of the tube," explains Dr. Wenzel Novak, global senior director business development at Gerresheimer. Another advantage of the plastic is its high impact strength. It protects the adapter from damage, for example in the event of impacts.
Two functions in one component
The system comprising an adapter and a closure is produced by two-component injection molding as a hard-soft combination. First the adapter is molded from copolycarbonate, then the cap is injection-molded from a thermoplastic elastomer. "The hard thermoplastic and the soft elastomer parts bind strongly to each other. There is no adhesive required, so there are no chemical reactions that could cause increased torque," explains Dr. Martin Doebler, medical technology specialist at Covestro.
The combination of closure and adapter in one component simplifies the manufacturing process and means greater cost-effectiveness. The person using the syringes also benefits: they only have to mount one connected part on the syringes. Turning the cap to open the syringes releases tabs that spread and prevent the cap from closing again. This means that the syringe cannot be opened and closed unnoticed. This tamper-evident feature prevents misuse of the systems and counterfeit products with regard to medicines.
Support in material selection, application technology and processes
Covestro provided Gerresheimer with extensive support during the development of the complex component – including recommendations on the correct choice of material and technical application advice. In addition, experts from the polymer manufacturer were on hand to provide advice and assistance in the design of the manufacturing process.
Apec® 1745 is no "stranger" in medical technology. “The biocompatible material meets the requirements of the ISO 10993-1 standard for the biological evaluation of medical devices,” says Barbara Giershausen, key account manager for Gerresheimer. "It is used, for example, to manufacture films for special filter housings and respiratory masks.”
About Covestro LLC:
Covestro LLC is one of the leading producers of high-performance polymers in North America and is part of the global Covestro business, which is among the world’s largest polymer companies with 2017 sales of EUR 14.1 billion. Business activities are focused on the manufacture of high-tech polymer materials and the development of innovative solutions for products used in many areas of daily life. The main segments served are the automotive, construction, wood processing and furniture, electrical and electronics, and medical industries. Other sectors include sports and leisure, cosmetics and the chemical industry itself. Covestro has 30 production sites worldwide and employed approximately 16,200 people at the end of 2017.
Find more information at www.covestro.us.
Covestro Contact:
Lauren West, Phone: +1 412 413 4141
Lauren.West@covestro.com
rei/ro (2018-153E)
Apec® is a registered trademark of the Covestro group.
# # #
This news release may contain forward-looking statements based on current assumptions and forecasts made by Covestro AG. Various known and unknown risks, uncertainties and other factors could lead to material differences between the actual future results, financial situation, development or performance of the company and the estimates given here. These factors include those discussed in Covestro’s public reports which are available at www.covestro.com. The company assumes no liability whatsoever to update these forward-looking statements or to conform them to future events or developments.
Editor’s Note: Follow news from Covestro on Twitter:
www.twitter.com/covestro