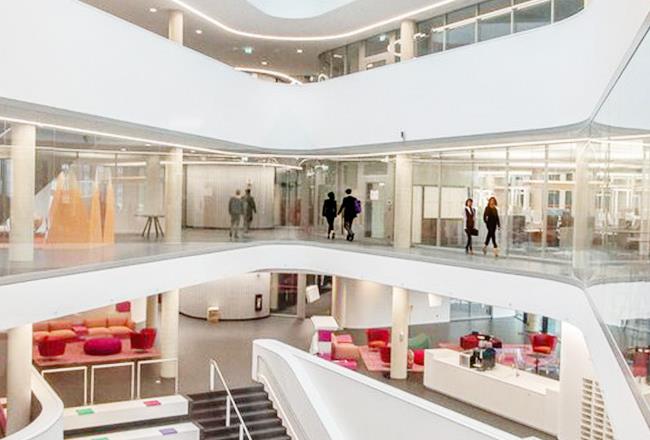
Covestro als Unternehmen: gemeinsam für mehr Zirkularität
Polymere oder Kunststoffe sind aus dem modernen Leben nicht mehr wegzudenken und für die Gestaltung einer wirklich nachhaltigen Zukunft unverzichtbar. Deshalb entwickeln wir Stoffe, die in vielen Schlüsselsektoren auf dem Weg zu Kreislaufwirtschaft und Klimaneutralität unerlässlich sind. Unsere Innovationskraft und unser Streben nach Nachhaltigkeit befähigen uns dazu, ständig neue Produktideen zu entwickeln. Dabei müssen wir manchmal große Herausforderungen meistern, doch genau dadurch wissen wir auch, dass wir auf dem richtigen Weg sind.
Neugierde ist Teil unserer DNA. Wenn auch Sie neugierig sind, können Sie gleich hier mehr über uns erfahren.
Konzernkennzahlen 2024
€
1
Mrd.
Konzernumsatz
€
1
Mrd.
EBITDA
€
1
Mio.
Free Operating Cash Flow
1
Mio. t
Treibhausgasemissionen*
1
Mitarbeitende
1
Produktionsstandorte weltweit
*Gemessen an CO2-Äquivalenten (Scope 1 & 2)
Eine Ausrichtung mit klarem Fokus
Wir bieten eine breite Palette von Produkten und Dienstleistungen für unterschiedliche Märkte, Anforderungen und Branchen. Aus diesem Grund haben wir unser Portfolio nach Geschäftsspezifika und Kundenbedürfnissen gegliedert.
Die beiden übergeordneten Segmente sind „Performance Materials“ und „Solutions & Specialties“. Sie bestehen aus insgesamt sieben Geschäftseinheiten. Jede Geschäftseinheit ist mit Blick auf die für sie maßgeblichen Erfolgsfaktoren organisiert und integriert alle geschäftskritischen Aktivitäten entlang der Wertschöpfungskette.
Darüber hinaus verfolgen wir bestimmte unternehmensübergreifende „Aufbauaktivitäten“ zur Sicherung unserer langfristigen Entwicklung. Dazu gehören die Bereiche Nachhaltigkeit, Innovation, Digitalisierung und Strategie.
Das Warum und das Wie
Die Frage „Warum tun Sie das, was Sie tun?“ ist häufig nicht leicht zu beantworten. Bei Covestro haben wir jedoch eine Antwort gefunden und möchten sie mit Ihnen teilen: Wir sind überzeugt, dass ein Unternehmen nicht allein durch seine Produkte, sondern vielmehr durch seinen ganzheitlichen Handlungsrahmen definiert wird.
Was hat es mit unserer Strategie „Sustainable Future“ auf sich?
Die Klimakrise zwingt ganze Branchen dazu, sich anzupassen. Bei Covestro möchten wir uns jedoch nicht einfach anpassen, sondern proaktiv an einer kreislauforientierten Zukunft arbeiten. Mit unserer Strategie „Sustainable Future“ machen wir unser Unternehmen zu einem Teil der Lösung für die Herausforderungen unserer Zeit – wir stehen in der Verantwortung. Erfahren Sie mehr über die drei Säulen!
Die Besten werden, die wir sein können
Die Ausschöpfung des eigenen Potenzials ist die Grundlage für einen kontinuierlichen und profitablen Unternehmenserfolg. Bei Covestro streben wir ständig danach, unsere Kundenorientierung, Effizienz und Wettbewerbsfähigkeit zu maximieren. Unsere klare Organisationsstruktur, die wir im Jahr 2021 eingeführt haben, war dafür ein wichtiger Schritt.
Nachhaltiges Wachstum fördern
Wir arbeiten zielgerichtet daran, unser Produktportfolio noch stärker auf Nachhaltigkeit und im Sinne der Kreislaufwirtschaft auszurichten. Anhand der Nachhaltigkeitsbewertung unseres Produktportfolios (Portfolio Sustainability Assessment, PSA) – basierend auf der Methodik des globalen Nachhaltigkeitsforums „World Business Council for Sustainable Development“ (WBCSD) – baut Covestro ein zukunftssicheres, innovatives und nachhaltiges Produktportfolio auf. Dazu werden Entwicklungen im regulatorischen Umfeld und im Marktumfeld mithilfe der PSA frühzeitig identifiziert und in Entscheidungsprozesse einbezogen. Die Ergebnisse der PSA sollen in Entscheidungen bezüglich des Produktportfolios sowie in Bezug auf die Unternehmenssteuerung integriert werden. Die Ergebnisse des Pilotprojekts zur Bewertungsmethode werden derzeit genutzt, um die Methode in Zusammenarbeit mit einem externen Anbieter weiter zu optimieren und beispielsweise Aspekte der Kreislaufwirtschaft, der Klimaneutralität und der gesellschaftlichen Auswirkungen tiefer zu integrieren. Die weitere Pilotierung und der externe Review der Methode sollen im Jahr 2024 abgeschlossen werden.
Darüber hinaus investieren wir in Marktsegmente, die langfristig attraktiv und umweltfreundlich sind. In Zukunft werden wir darüber hinaus all unsere wachstumsfördernden Aktivitäten (z. B. unsere Venture Capital Initiative) noch stärker auf Nachhaltigkeit ausrichten.
Bis 2025 sollen 80 % unserer Ausgaben für Forschungs- und Entwicklungsprojekte zur Erreichung der Ziele für nachhaltige Entwicklung der Vereinten Nationen (Sustainable Development Goals – SDGs) beitragen. Stand Ende 2022 lag dieser Wert bei 51 %.
Vollständige Kreislaufwirtschaft erreichen
Wenn wir die Kreislaufwirtschaft fördern wollen, müssen wir bei uns selbst anfangen. Covestro will eine vollständige Kreislaufwirtschaft erreichen – und die Schritte auf dem Weg dorthin sind in unserem globalen Programm „Circular Economy“ festgelegt. Das Programm konzentriert sich auf die Verwendung alternativer Rohstoffe und erneuerbarer Energien sowie auf die Förderung innovativer Recyclinglösungen und Partnerschaften.
Langfristig arbeiten wir daran 100 % unserer Produkte aus alternativen Rohstoffen herstellen, um uns von fossilen Ressourcen wie Rohöl zu befreien. Durch die Neuausrichtung unserer Produktion werden wir in der Lage sein, Rohstoffe aus Biomasse und recycelte Komponenten zu verwenden.
Im Jahr 2022 wird Covestro über 55.000 Tonnen erneuerbare Rohstoffe beziehen und verarbeiten.
Für die Kreislaufwirtschaft spielt Klimaneutralität eine entscheidende Rolle. Das bedeutet, dass unser Handeln keine negativen Auswirkungen auf das Klima haben darf – das gilt auch für die Produktion des Unternehmens. Wir streben an, bis 2035 hinsichtlich der Treibhausgasemissionen aus unserer eigenen Produktion und der Energie, die wir von Lieferanten beziehen, klimaneutral zu werden.
Das Ziel unseres globalen Klimaprogramms ist es, alle Produktionsstandorte mit 100 % erneuerbarer Energie zu betreiben. Wussten Sie, dass bereits 45 % des Stroms an unserem Standort in Antwerpen (Belgien) aus erneuerbaren Energien stammen?
Grenzen zu verschieben, ist Teamarbeit. Deshalb rufen wir weltweit Partnerschaften und Netzwerke ins Leben.
Möchten Sie mehr erfahren? Mit Vergnügen! Lesen Sie mehr über Covestro und Nachhaltigkeit.
Ein solides Fundament: Digitalisierung und Kultur
Unsere Strategie „Sustainable Future“ stützt sich auf ein solides Fundament: unsere „We Are 1“-Kultur und die umfassende digitale Transformation, die wir konsequent auf mehreren Ebenen vorantreiben. Dazu gehört, dass wir das Potenzial der künstlichen Intelligenz nutzen und unsere digitalen Forschungs- und Entwicklungsaktivitäten ausbauen, indem wir zum Beispiel mit internationalen Technologieunternehmen wie Google zusammenarbeiten. Außerdem setzen wir Algorithmen und maschinelles Lernen gewinnbringend ein, unterstützt durch wertvolle Erkenntnisse aus der Datenwissenschaft.
Was unsere Mitarbeiter betrifft, so möchten wir, dass sie den Status quo hinterfragen und neue Geschäftsansätze entwickeln. Uns ist klar, dass dies nur in einem offenen und integrativen Klima möglich ist. Deshalb haben wir die Unternehmenskultur „We Are 1“ geschaffen, die von jedem einzelnen unserer Mitarbeiter mit Leben erfüllt wird und auf unseren einzigartigen Werten basiert: Wir sind neugierig, mutig und vielfältig.
Zweck
Klimawandel, wachsende Weltbevölkerung, Urbanisierung: Diese und viele andere globale Trends stellen die Menschheit vor große Herausforderungen – bereits heute und erst recht morgen. Covestro trägt mit seinem umfassenden Sortiment an innovativen Produkten und Lösungen dazu bei, diese Herausforderungen zu meistern. Hochwertige Kunststoffe sind ein Schlüssel zu einer ökologischen und damit besseren Zukunft für die kommenden Generationen.
Unser Zweck gibt die Richtung unseres Handelns vor. Wir müssen unser Engagement und unsere Verantwortung für die Bewahrung der natürlichen Lebensgrundlagen mit der Schaffung dauerhafter Werte verbinden.
Vision
Die Wirtschaft von heute ist oft eine Einbahnstraße: Abbauen, herstellen, wegwerfen – dieses jahrzehntelange Prinzip hat ausgedient. Bei Covestro wollen wir deshalb eine vollständige Kreislaufwirtschaft erreichen und möchten dazu beitragen, sie zu einem globalen Leitprinzip zu machen.
Kreislaufwirtschaft ist der Schlüssel zu Klimaneutralität, Ressourcenschonung und der Bewahrung von Natur und Umwelt. Deshalb ermutigen wir jeden Einzelnen, dazu beizutragen, durch folgende Aktivitäten den Kreislauf zu schließen:
- Neue Wege finden, um Ressourcen sinnvoll zu nutzen und wiederzuverwenden
- Produkte herstellen, die so lange wie möglich halten
- Abfall vermeiden
- Produkte als Ressource für das Recycling betrachten
- Alternative Quellen für umweltfreundliche Rohstoffe erkunden (z. B. Biomasse)
Strategie
Wenn man ein Ziel erreichen will, braucht man eine Strategie. Unsere Strategie heißt Sustainable Future. Sie umfasst drei strategische Säulen: das Unternehmen so transformieren, dass es sein volles Potenzial ausschöpfen kann, auf rentable Weise Nachhaltigkeit erreichen und die vollständige Kreislaufwirtschaft umsetzen.
Diese Strategie möchten wir mit der Kraft einer beschleunigten digitalen Transformation und durch die Ausweitung unserer „We Are 1“-Kultur umsetzen. Sie möchten weitere Informationen erhalten? Erfahren Sie mehr über unsere Strategie „Sustainable Future“ und konkrete Maßnahmen!