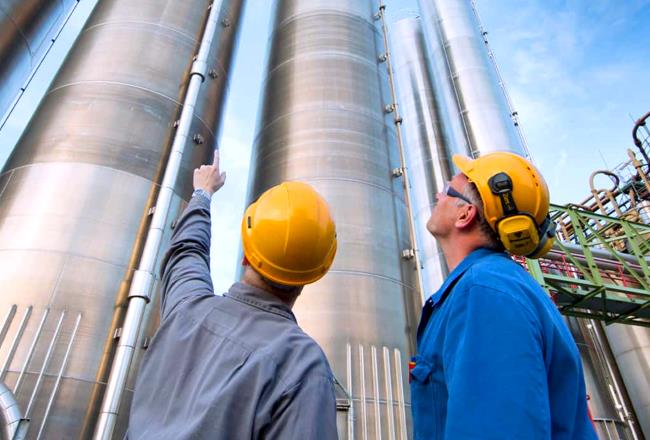
High-tech made in Krefeld-Uerdingen
Nearly 1,050 employees work in Krefeld-Uerdingen every day. The majority of them work in production. Their tireless effort is one reason for the company's success. Covestro manufactures a variety of raw materials for industrial applications and everyday objects at a total of nine production plants. From smartphones to cars to refrigerators: they all carry a piece of “Krefeld-Uerdingen” inside of them.
Innovative materials for everyday use
The German sites account for around 30 percent of global production capacity – a significant proportion of which comes from NRW. Krefeld-Uerdingen, Leverkusen and Dormagen from a strong site network. They jointly organize maintenance, infrastructure, logistics, warehousing and services.
Krefeld-Uerdingen was the first site to implement many innovative and sustainable production processes at an industrial scale. The site is closely associated with production of polycarbonate. This material was first invented in Krefeld-Uerdingen by Hermann Schnell in 1953 – and continues to enrich the lives of millions of people worldwide under the brand name Makrolon®. It is used, for instance, in laptop-housings, eyeglass lenses, suitcases, and hard hats. The automotive industry also relies on this versatile material to manufacture vehicle headlights and chassis parts for example. Thanks to polycarbonate, the end products are now not only more impact-, scratch-, and weather-resistant but also significantly lighter.
Another focus of production at the site is methylene diphenyl diisocyanate (MDI) – a precursor for high-quality foams. Once processed into a soft foam, MDI is used in products such as mattresses, furnishings and vehicle seats. As a rigid foam, it delivers insulation solutions for buildings and refrigerating devices. The MDI production system in Krefeld-Uerdingen has a capacity of over 220,000 tons per year. It can offer MDI products in around 130 variations, all of which are made safely and efficiently in Krefeld-Uerdingen.
Award for high standard of sustainability
Covestro has had Krefeld-Uerdingen certified to the recognized ISCC Plus mass balance standard - and is one of the world's first production sites to do so. This enables the company to offer its customers innovative raw materials that are verifiably derived from renewable sources and have the same quality as their fossil counterpart. Certified polycarbonate and the precursor MDI are among the products available at the site.
The gradual switch to alternative raw materials from renewable sources is part of the company-wide circular economy strategy. With the ISCC Plus mass balance certification, Covestro is demonstrably a step closer to its vision of climate-neutral production. After all, the use of alternative raw materials is an important step toward reducing its own CO₂ footprint.
For Covestro, climate-neutral raw materials are an important factor in achieving its own sustainability goals. In the long term, the company therefore intends to align its entire production and product range exclusively to the concept of the circular economy and the progress of climate protection. Covestro will offer every product in a climate-neutral version in the future.
Already today, Covestro is steadily expanding its portfolio: One pioneering example is the world's first climate-neutral* polycarbonate. It is produced at the Krefeld-Uerdingen site using raw materials from mass-balanced biowaste and residual materials as well as renewable energy. The climate-neutral* polycarbonate - which also includes selected Makrolon® RE grades - has the same good quality and performance as its fossil-based counterpart. It is the first choice for all customers looking for alternative raw materials with a lower CO₂ footprint.
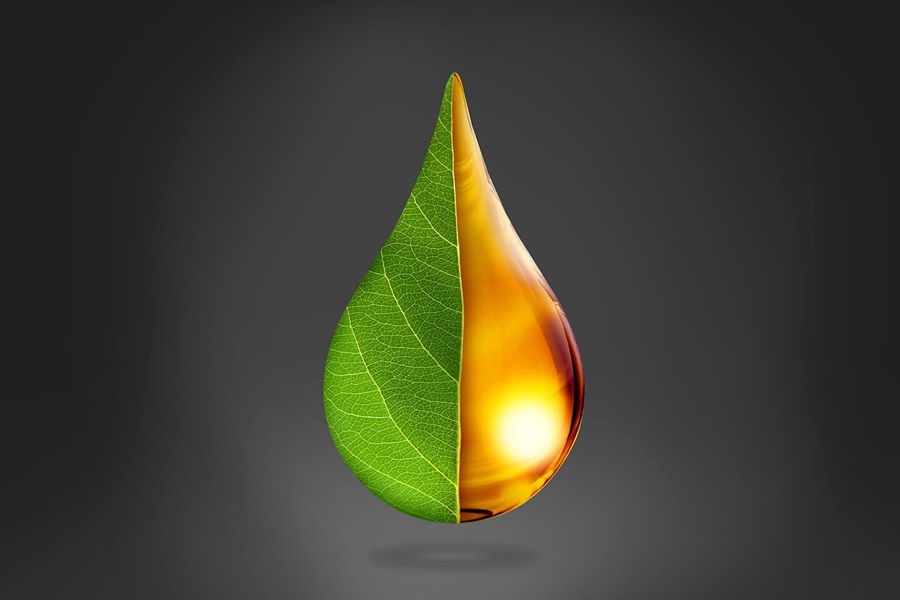
* Climate neutrality is the result of an internal assessment of a partial product life cycle from raw material extraction (cradle) to the factory gate (Covestro gate), also known as cradle-to-gate assessment. The methodology of our life cycle assessment, for which external verification and certification will be available shortly, is based on ISO standards 14040 and ISO 14044. The calculation takes into account biogenic carbon sequestration based on preliminary data from the supply chain. No compensation measures have been applied.
Since 2021, Covestro's product portfolio also includes a climate-neutral* methylene diphenyl diisocyanate (MDI). It is an indispensable raw material - for example for the production of innovative polyurethane insulating panels and sandwich panels. These have proven themselves worldwide as highly efficient elements in the thermal insulation of buildings. The use of polyurethane insulation can reduce heating or cooling requirements by up to 70 percent.
Covestro's sustainable MDI grades are climate-neutral* from the cradle to the factory gate. This is made possible by the use of alternative raw materials - based on plant waste - which are attributed to the products with the help of certified mass balancing according to ISCC PLUS. The climate-neutral* MDI and its precursors are produced at the Krefeld-Uerdingen site.
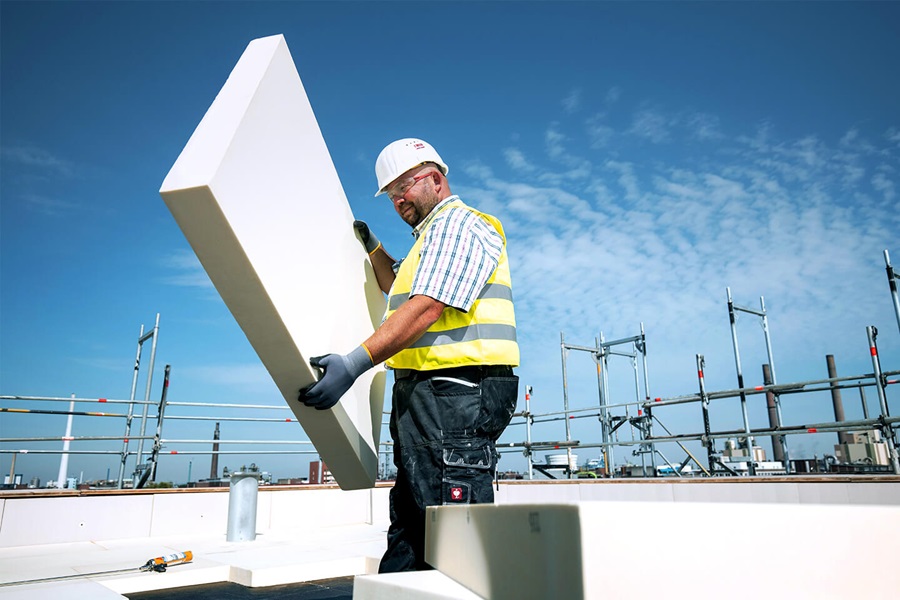
* Climate neutrality is the result of an internal assessment of a partial product life cycle from raw material extraction (cradle) to the factory gate (Covestro gate), also known as cradle-to-gate assessment. The methodology of our life cycle assessment, for which external verification and certification will be available shortly, is based on ISO standards 14040 and ISO 14044. The calculation takes into account biogenic carbon sequestration based on preliminary data from the supply chain. No compensation measures have been applied.
Covestro and LANXESS are cooperating on the energy-intensive production of chlorine, caustic soda and hydrogen at the three NRW sites. These basic raw materials form the basis for many products in the chemical industry. Thanks to the close cooperation, both companies can make the manufacturing process significantly more climate-friendly.
Covestro supplies LANXESS with chlorine, caustic soda and hydrogen from Leverkusen, Dormagen and Krefeld-Uerdingen - around one-third of which will be produced in the future using energy from hydropower based on certificates of origin.
The specialty chemicals company uses the basic raw materials supplied by Covestro, among other things, for products that go to the food industry or agriculture after further processing. The cooperation will reduce indirect emissions by around 120,000 metric tons of CO₂ equivalents per year.
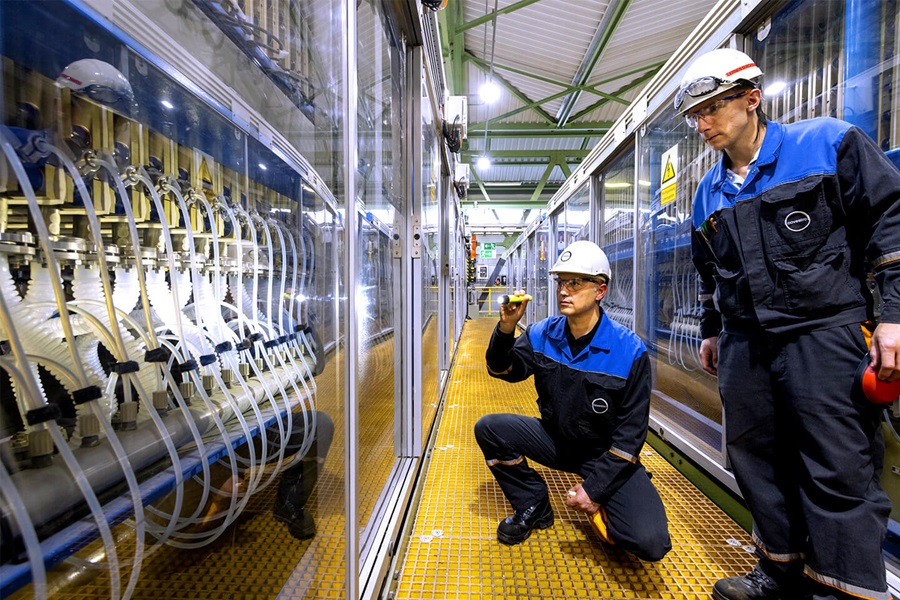
Sustainability is also a top priority at Covestro's site in Krefeld-Uerdingen – for instance, in chlorine production. Chlorine, for example, is used in around two-thirds of all chemical products, including plastics. Unfortunately, chlorine is not found in nature and has to be produced through an energy-intensive process.
Covestro and its partners are helping to change that: the company has developed a process that reduces the required amount of electricity by up to 25 percent. The oxygen depolarized cathode (ODC) method has been used successfully at the Krefeld-Uerdingen site since 2011.
That innovation was based on the commonly used membrane process in chlor-alkali electrolysis, which has become a standard method for manufacturing chlorine. In this process, chlorine, sodium hydroxide and hydrogen are derived from table salt (NaCl) and water. Krefeld-Uerdingen will now no longer use customary hydrogen-producing electrodes but rather an oxygen depolarized cathode. Supplying the cathode with oxygen prevents the formation of hydrogen, leading only to the production of chlorine and sodium hydroxide. Compared to the standard method, a significantly lower electrical voltage is required and the energy consumption is reduced by up to 25 percent.

During a major shutdown of several plants in 2020, the chlorine production capacity was increased - by a 52,000 metric tons per year. This was made possible by two additional electrolysers. They also operate with innovative ODC technology. Covestro is thus underlining once again its ambitious sustainability goals at the site.
In 2022, Covestro has launched another production line for the manufacture of refined plastics in Krefeld-Uerdingen. The site is responding to increased market demand, particularly from the automotive industry. This has increased the site's total capacity by around a third and raises the number of production lines to nine.
The heart of the new production line for compounding polycarbonate is a ten-meter-long extruder. In it, the polycarbonate melt, which has previously been provided with different additives and colors, is mixed at high temperatures and then pressed out – like in a meat grinder. The resulting refined products make the Covestro site in Krefeld-Uerdingen ready for the future.
During the project, three additional silos – among other plant sections – were built. A new underwater pelletizer, which extends over several floors in the building, was also newly built. Further additions include a conveyor system with various pipes, several mixing silos and a filling line for 25 kilo bags.
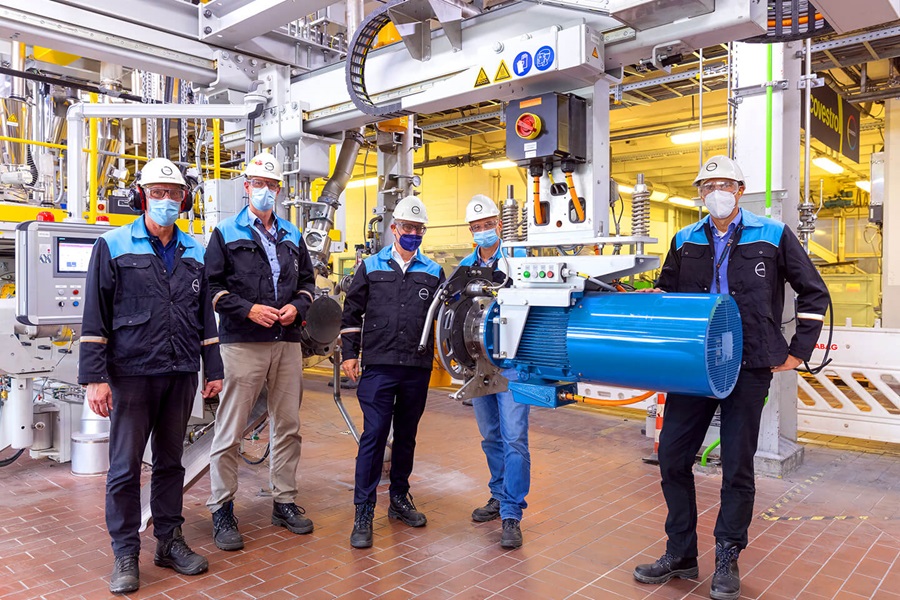
In Krefeld-Uerdingen, Covestro has succeeded in reusing the salty industrial wastewater that is produced through polycarbonate manufacture in an industrial pilot plant for the first time. This will save up to 15,000 tons of salt and 200,000 tons of fully desalinated water per year. Since the recycled waste water can be reused in chlorine production, this process also saves valuable drinking water resources.
Covestro intends to develop new approaches to transforming the supply of raw materials, among other things. The recycling of salty industrial wastewater is one of them. The roll out of the technology to other Covestro sites is also ongoing. Currently, researchers continue to work intensively on multiple projects and procedures or using wastewater containing salt and increasing the quantity of recycled materials.
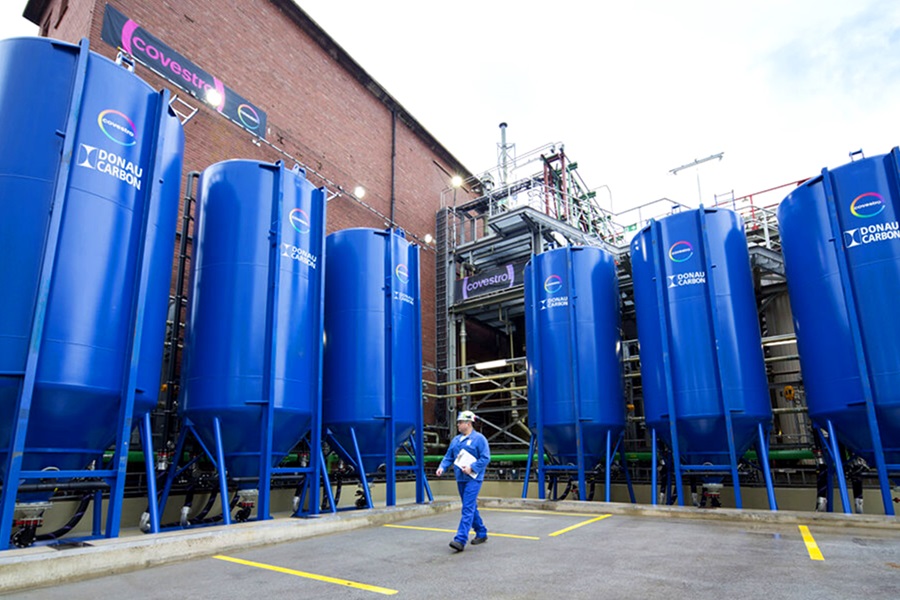
Covestro has pushing digital innovation forward for many years. The company continues to drive progress towards Industry 4.0. Digitalization also plays a major role at the Krefeld-Uerdingen site. This is particularly evident in the mobile maintenance of production facilities – the so-called "mobile maintenance".
It enables simplified and automated plant maintenance through digital tools. They collect the production data of the plants and evaluate it reliably. Anything that would have previously been recorded in writing is now handled digitally. This not only saves time and money, but also harmonizes the individual production steps and thus ensures more sustainable process flows.
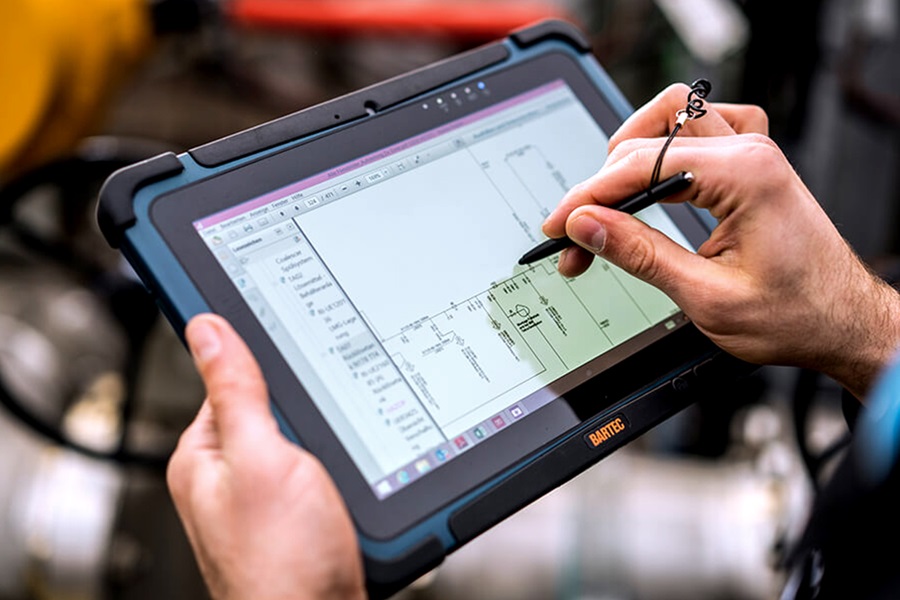
With its innovative and climate-friendly products and processes, the Covestro Krefeld-Uerdingen site is delivering key solutions for the global challenges of our time. The company is always looking for new ways to incorporate sustainability to help make the world a brighter place. Covestro intends to continue pursuing the path it has set out in Krefeld-Uerdingen – and is already thinking today about tomorrow.
Covestro is aiming for operational climate neutrality by 2035. By then, net-zero emissions from our own production (Scope 1) and from purchased energy (Scope 2) are to be achieved. Upstream and downstream greenhouse gas emissions in the value chain (Scope 3) are also to be significantly reduced by 2035 – in the long term, Covestro aims to achieve climate neutrality for Scope 3 emissions by 2050.
Covestro – A good neighbor
Living together in harmony is very important to Covestro. This is why the company actively seeks out dialog and maintains close contacts with neighbors at its production locations.
Safety
At Covestro, safety comes first. The company is dedicated to reducing risks for its employees and neighbors and to ensuring safe production sites. Additional information is available on the Chempark Krefeld-Uerdingen website.