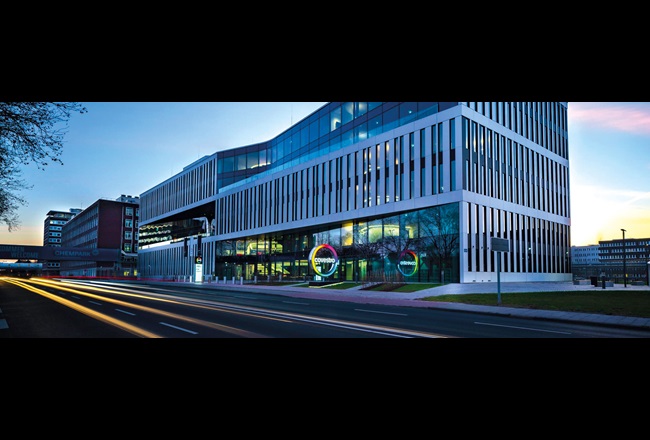
Home base in Leverkusen
Nearly 3,600 employees work for Covestro in Leverkusen in administration, research and production. They ensure safe, environmentally friendly and highly efficient operation with outstanding commitment and broad expertise. New technologies and processes are used in the large production facilities at the site. These help make processes even more efficient.
At the same time, Covestro's innovations set new standards for sustainability – even beyond the company's own boundaries. Since 2015, Covestro has invested around 1.1 billion euros in its plants in order to further ensure that Leverkusen remains a successful production site long-term.
1
employees
(FTE)
1
young professionals
1 bn
bn
euros invested since 2015
The German sites account for around 30 percent of global production capacity – a significant proportion of which comes from NRW. Leverkusen, Dormagen and Krefeld-Uerdingen have formed a site network since 2010. They are all located within 70 kilometers of one another and organize maintenance, infrastructure, logistics, warehousing and services. This results in more streamlined processes, more efficient production and better cost-competitiveness.
Certification for high sustainability standards
Since 2022, the Leverkusen site has also held the internationally recognized ISCC Plus mass balance certification. As a result, the company can supply its customers with large product volumes made from renewable attributed raw materials. The selected polycarbonates, components for polyurethane (PU) coatings and adhesive raw materials are characterized by equally good quality and properties as their fossil-based counterparts.
Thanks to the ISCC Plus mass balance certification, Covestro is once again one step closer to its ambitious goals: to become operationally climate-neutral by 2035 and achieve net-zero emissions from its own production (Scope 1) and from purchased energy (Scope 2). Upstream and downstream greenhouse gas emissions in the value chain (Scope 3) are also to be significantly reduced by 2035 – in the long term, Covestro aims to achieve climate neutrality for Scope 3 emissions by 2050.
Birthplace of high-tech plastics
Leverkusen is also home to research laboratories and an upscaling plant. Everything started with one outstanding innovation. In 1937, chemist Otto Bayer discovered the plastic polyurethane in Leverkusen, a material that is now essential in many everyday applications.
We use it everyday as a soft foam, in the form of mattresses, soft furniture and vehicle seats. As a rigid foam, it is used in home insulation to keep heat outdoors in the summer and indoors in the winter. It ensures that the food in our refrigerators stays fresh. Polyurethane also serves as the basis for the coatings, adhesives, and sealants required in many different sectors such as the automotive industry and the construction sector.
World’s first pilot plant for bio-based aniline
In Leverkusen, a hotbed of innovation, Covestro is moving forward with the implementation of a unique process for producing the important chemical aniline for the first time entirely based on plant biomass instead of petroleum. For this purpose, the plastics manufacturer put a special pilot plant into operation at the beginning of 2024. Larger quantities of bio-based aniline are produced at this plant with the aim of further developing the new technology for production and transferring it to an industrial scale.
Aniline is a true all-around performer in the chemical industry and an important raw material used in medications and dyes. It also serves as a key raw material for foams that insulate buildings and refrigerating devices. To date, aniline has been produced from fossil raw materials such as petroleum. With the new process, Covestro is advancing the development of a circular, bio-based economy.
This multi-award-winning process was developed by Covestro and its scientific partners. Compared to conventional technology, the process leads to a significantly improved CO₂ footprint of aniline. The RWTH Aachen University with the research facility CAT Catalytic Center as well as the University of Stuttgart with its Technology Transfer Initiative are also participating in the project.
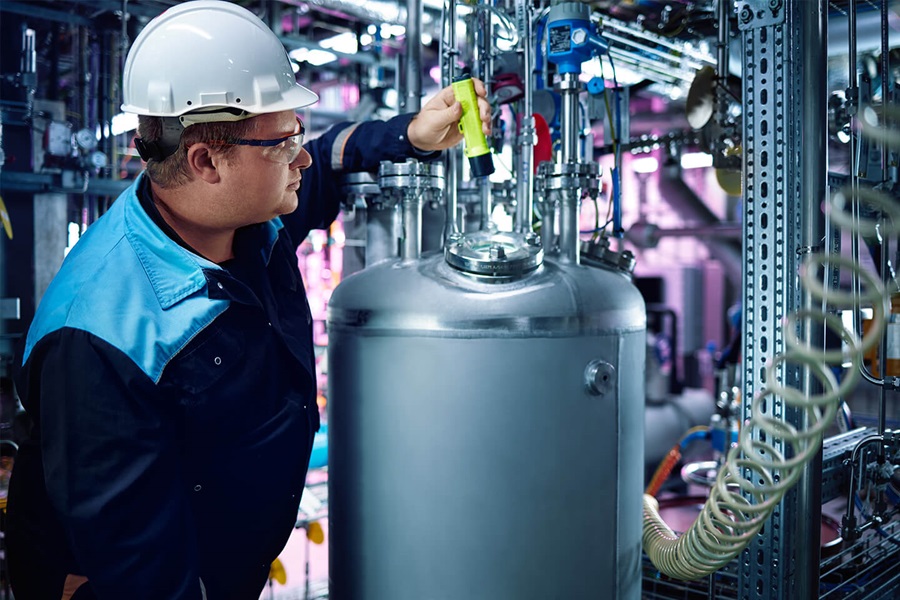
Pilot plant for chemical recycling
For Covestro, plastic waste is a valuable raw material. That is why the company makes innovative recycling a priority. Covestro is continuously developing new processes under the name "Evocycle® CQ”. The first initiative is called Evocycle® CQ Mattress: Together with partners, Covestro has developed an innovative technology for the chemical recycling of flexible polyurethane (PU) foam from used mattresses.
It is currently tested in a pilot plant at the company’s site in Leverkusen. The aim is to validate laboratory results, optimize the process and develop products and applications on a small industrial scale. The innovation enables Covestro to recover both main components: the polyol and the toluene diamine (TDA) – a precursor of toluene diisocyanate (TDI). In this way, the used mattresses are recirculated and given a second life through chemical recycling.
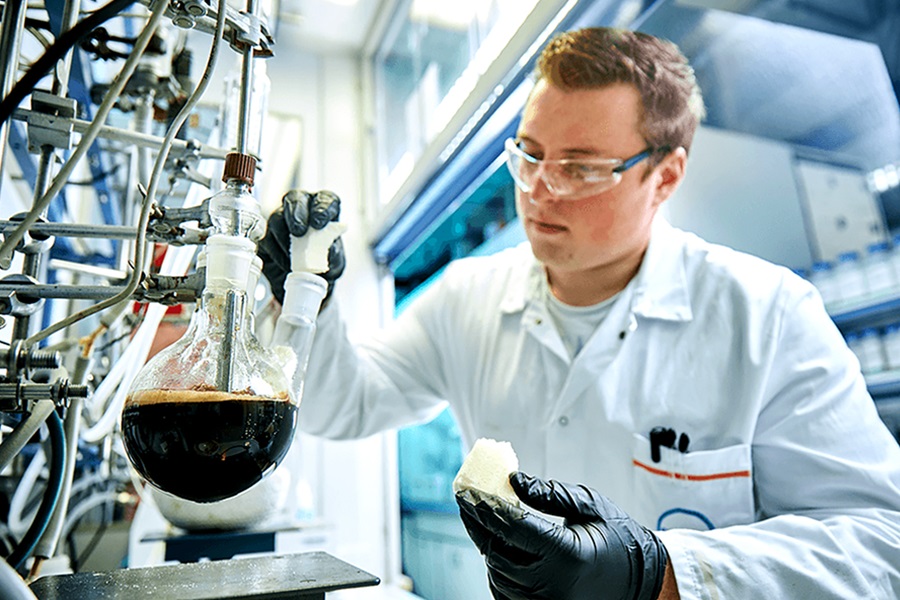
With chemical recycling, plastics are broken down chemically into their original molecular forms so that they can be processed into entirely new plastic materials. It is the only way to recycle certain plastics in relevant quantities. There is an increasing demand for new developments in this area - and this is where Covestro can apply its core chemical expertise.
It is an important step towards a closed recycling loop. This not only opens up new business areas, but also makes a significant contribution to more sustainable waste management and to protecting the climate and the Environment..
Electrolysis with renewable electricity from hydropower
On the path to operational climate neutrality in 2035, Covestro plans to switch its production entirely to electricity from renewable sources. This will also make the energy-intensive production of basic raw materials more climate-friendly. The company has already taken a first step: Covestro is now cooperating with LANXESS in the production of chlorine, caustic soda and hydrogen at its three NRW sites.
In the future, Covestro will provide the specialty chemicals company with these basic raw materials from Leverkusen, Dormagen and Krefeld-Uerdingen. Around one-third of the total volume will be produced using energy from hydropower on the basis of certificates of origin. Thanks to the cooperation, indirect emissions can be reduced by around 120,000 metric tons of CO₂ equivalents per year.
Chlorine, caustic soda and hydrogen are the basis for many products in the chemical and plastics industries. LANXESS utilizes them, for example, for products used in the food industry or agriculture.
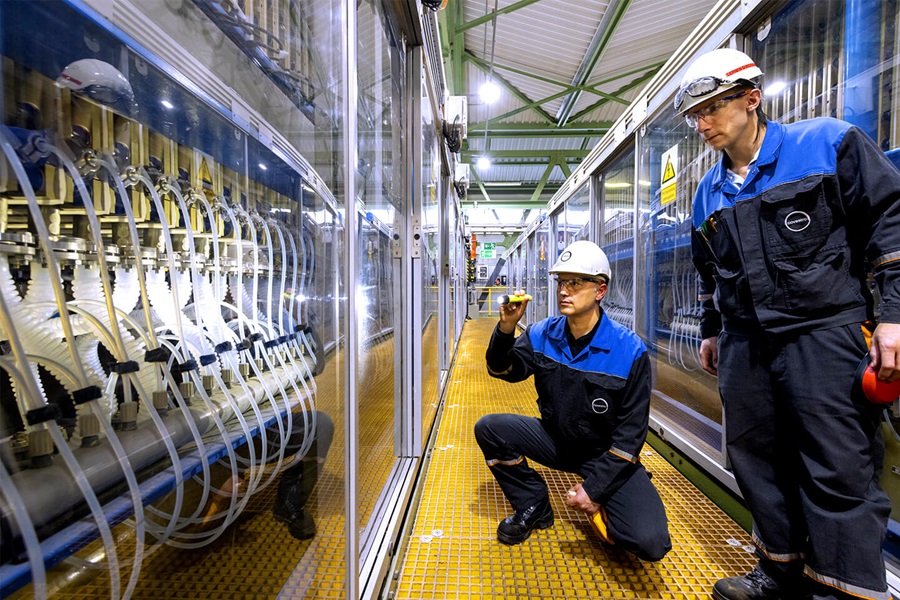
Digital upgrade for chlorine production
Digitalization is an important driver of innovation in the chemical industry. Industry 4.0 marks the start of a new era for companies in the sector. Covestro is actively seizing the opportunities offered by digitization. In Leverkusen and the two other NRW plants in Dormagen and Krefeld-Uerdingen, chlorine production has now been almost completely converted to a new, state-of-the-art cell voltage measurement system using fiber optic technology.
With more than 7,500 electrolysis elements, Covestro produces around 850,000 tons of chlorine annually in NRW, along with the by-products caustic soda and hydrogen. Digital measuring systems continuously monitor the cell voltages of each individual electrolysis element, ensuring smooth production around the clock. In this way, even the smallest deviations from the specified values are recorded in a fraction of a second and transmitted to computers via high-performance fiber optic cables.
Highly complex software then evaluates the electrical impulses within milliseconds. This new technology not only leads to a further increase in process reliability. It can also reduce the energy consumption of chlorine production – thus, the implementation of digitalization at Covestro contributes to climate-friendly production in this case as well.
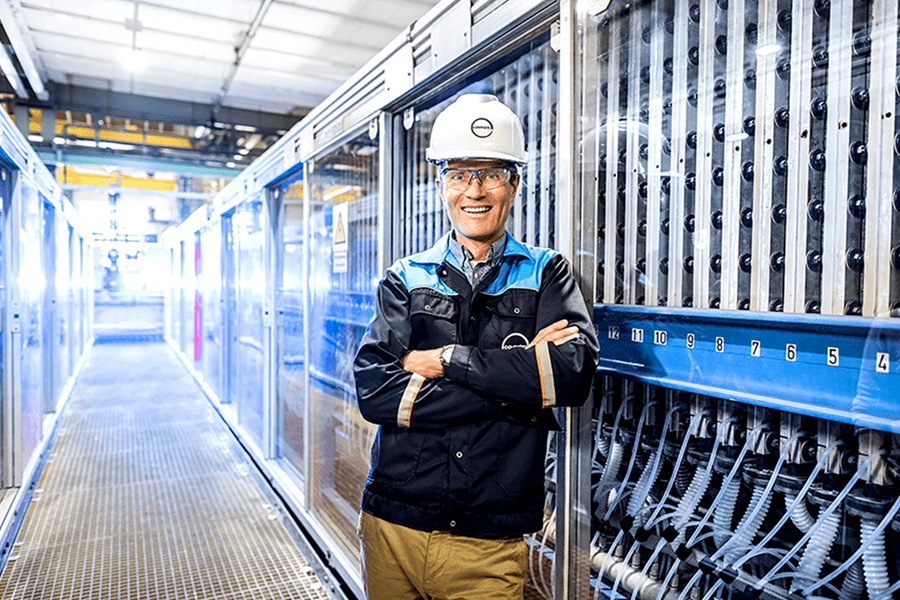
The headquarters completed in the fall of 2020 demonstrates the importance of the Leverkusen site for Covestro. The building offers space for around 700 employees and allows them to work in excellent conditions.
Covestro – A good neighbor
Living together in harmony is very important to Covestro. This is why the company actively seeks out dialog and maintains close contacts with neighbors at its production sites.
Safety
At Covestro, safety comes first. The company is dedicated to reducing risks for our employees and neighbors and to ensuring safe production processes. Additional information is available on the Chempark Leverkusen website.