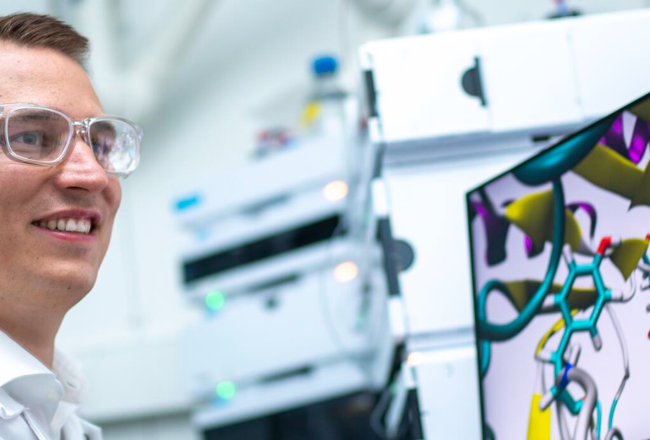
White Biotechnology for sustainable plastics
Green, white, red – the Italian flag probably springs to mind for many people. What might be less well known is that the three colors also play a role in a pioneering key technology: the use of microorganisms and enzymes that aim to advance different areas of modern life and drive innovation. While green biotechnology helps in agriculture, for example to make plants more resistant to climate change, red biotechnology advances medicine – for example to produce vaccines of the kind used to protect against coronavirus.
The third field is white or industrial biotechnology, which is increasingly used in the chemical and plastics industry. With microorganisms and enzymes, which are components of them, complex chemical reactions can be significantly simplified or new chemicals that were previously unavailable can be produced. In addition, the processes often take place under milder conditions than with conventional technology: temperatures and pressures are lower, fewer potentially harmful organic solvents are required, and undesirable by-products can be avoided or reduced.
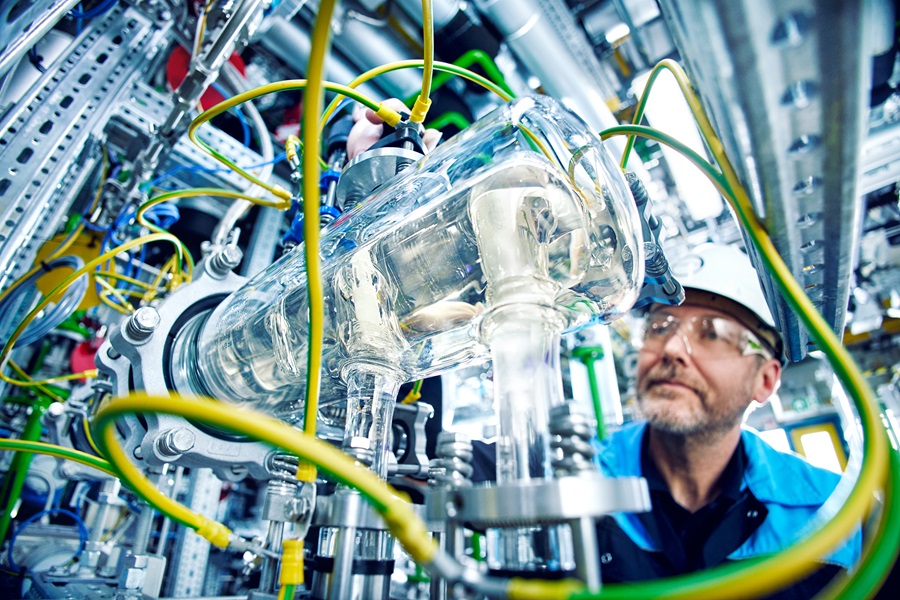
Own competence center
In order to leverage the potential of white biotechnology for plastics production, Covestro founded its own competence center in 2018. "We take nature as a model, which has produced sensational processes and has been practicing recycling for millions of years," says Dr. Gernot Jäger, who heads the facility. “With the help of enzymes and microorganisms, we can use alternative raw materials efficiently therefore replacing fossil resources. At the same time, unwanted by-products can be avoided or at least significantly reduced.”
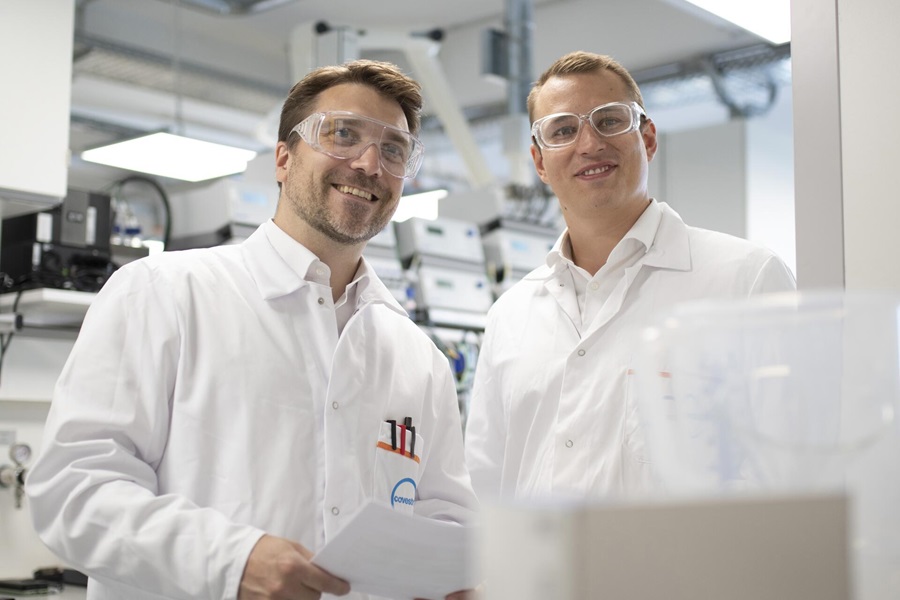
“We take nature as a model and use its tools in plastic production”
A newly modernized laboratory is now available to the biotech experts at Covestro's headquarters in Leverkusen. Here, biotechnological processes can be represented particularly realistically in a wide range of sizes - volumes from one milliliter to 100 liters will soon be possible.
In 2022, the competence center has been expanded to include a special research unit, the junior research group Enzyme Catalysis, or NEnzy for short. It will be funded over the next five years with 2.5 million euros in total from the German Federal Ministry of Education and Research and cooperates closely with RWTH Aachen University. From this, Covestro expects further impetus for the circular economy, on which the company is completely aligned.
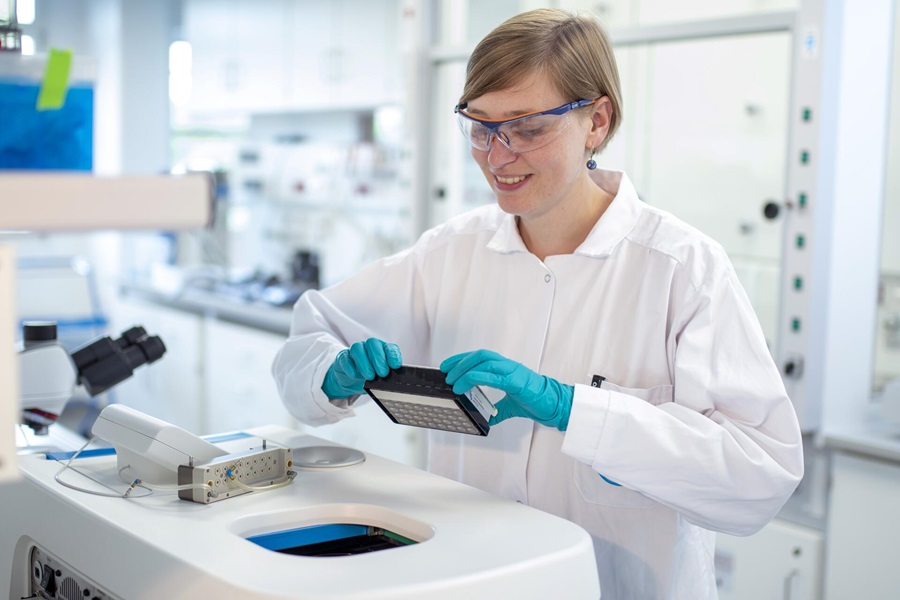
Biotechnology for plant-based chemicals
Covestro also uses industrial biotechnology to produce plastic components based on plant biomass instead of fossil raw materials. A central research and development project involves the important basic chemical aniline. To this end, the company and its partners have developed a process in which a tailor-made microorganism is used. This groundbreaking technology is now being tested and further developed in a special pilot plant at the Leverkusen site in Germany for industrial-scale production.
Another plastic component can already be produced on a similar scale based on plant biomass and with the help of white biotechnology: the precursor HDMA , which is used to manufacture paints and adhesives. Covestro and the US-based biotech company Genomatica have succeeded in doing this as part of a partnership.