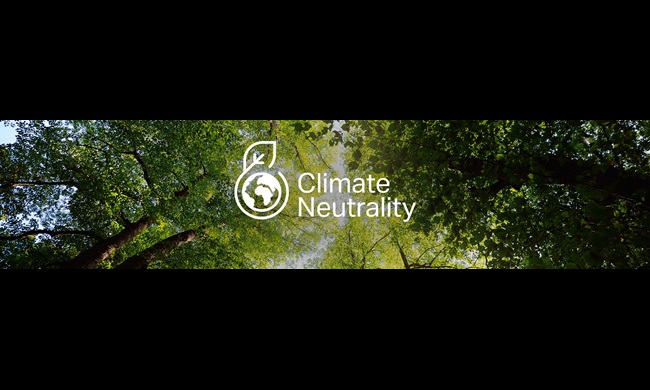
Our Scope 3 targets
We don't say it's easy – but possible. Together. Discover our complete climate neutrality targets. Read more
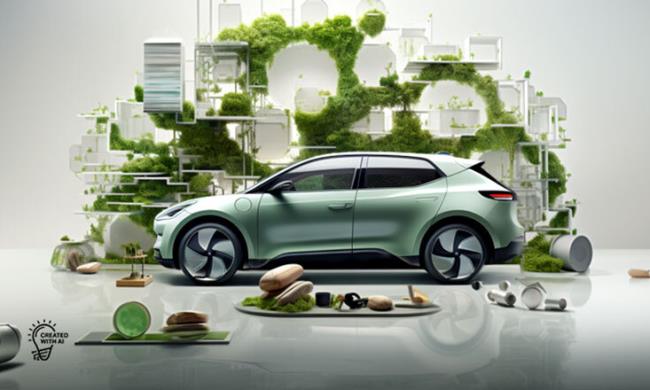
For sustainable mobility
Discover our innovative products and solutions for vehicles and infrastructure. Read more
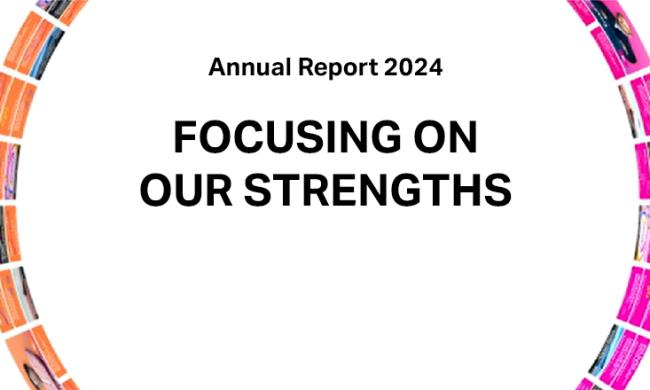
Annual Report 2024
Discover our annual report featuring highlights from 2024 and fascinating stories behind the numbers. Read more
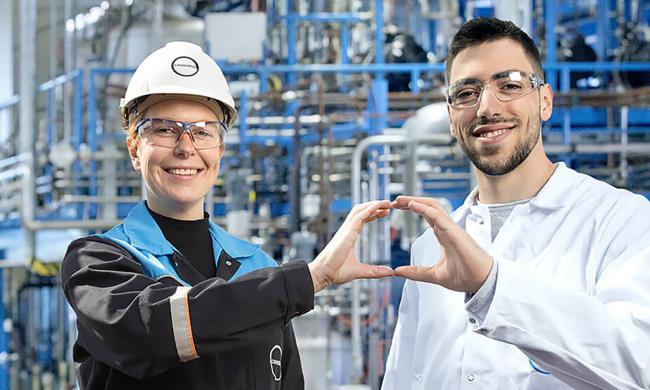
Circular Economy – Closing the Loop
Covestro wants to become fully circular and thus intends to accelerate the transformation to a climate-neutral and resource-conserving economy. Read more
Welcome to Covestro!
We are a world-leading manufacturer of high-quality polymer materials. With innovative products, processes and methods, we improve quality of life and drive our vision to become fully circular. Discover how Covestro's cutting-edge polymers drive progress in vital areas.
Your career at Covestro
Current job openings at our locations
Visit our career page
Shares
- Latest results (5)
- IR News (10)
- Financial Calendar (2)
https://annualreport.covestro.com/quarterly-statement-q1-2025/en/
https://annualreport.covestro.com/annual-financial-report-2024/en/
PDF [1.5MB]
PDF [.3MB]
https://covestro.com/en/investors/reports-and-presentations
July 11, 2025
June 24, 2025
May 6, 2025
March 18, 2025
February 26, 2025
January 8, 2025
December 19, 2024
December 16, 2024
December 12, 2024
July 31, 2025
October 30, 2025